|
|
National Medical Logistics Newsletter | |
|
|
Hopefully spring has finally arrived where you are and, like us, you are enjoying the sense of renewal that comes from this warmer, greener time of year.
With that in mind, our articles this month focus on introducing the concept and benefits of a healthcare centric Third Party Logistics services provider and the importance of integrating process flow charts as part of your Standard Operating Procedures. For more on these timely topics, read below.
National Medical Logistics
| |
What Is a 3PL?
Mention the acronym "3PL" and all sorts of images come to mind - a dark, dusty public warehouse storing consumer goods, electronics or automotive parts; an integrated parcel carrier like FedEx, UPS or DHL delivering packages around the world; possibly a few people with computer managing shipments, or maybe it's the company from whom your organization leases trucks. It is some of this and so much more.
Logistics service providers are the companies offering a singular logistical service around the physical movement of a product. These include airlines, steamship lines, freight forwarders, trucking companies, parcel carriers, couriers, public warehouse companies, leasing firms, etc. Those of us in supply chain management understand that product movement is only one of the three key processes to be managed. The other two are information and money.
By definition a 3PL is a company who specializes in managing some or all of the logistics of products, information and money between the seller of the product and it's buyers, and usually infers that two or more functions are managed concurrently i.e., warehousing and transportation. Increasingly, especially in non-healthcare industries, the 3PL is responsible for warehousing of its client's product, transportation into the warehouse or distribution center, management of all staff, inventory control, sales order processing, customer deliveries, replenishment of inventory; typically using its own specialized supply chain management technology.

To read more, click here. |
The Case for SOP's 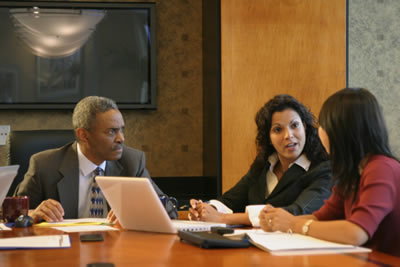
While it is important all healthcare stakeholders to develop and maintain Standard Operating Procedures (SOPs) it is also helpful to incorporate corresponding Business Process Flows. When these two components are combined it is NML's experience that the operating procedures can often be utilized as an effective training aid for new associates and to help shape or change upstream behavior. This can be especially useful as part of a new system implementation or as a precursor to ramping up for new business. They can also be used in support of implementing new supply chain strategies by showing associates their new tactical role for successful implementation of high-level objectives.
While not totally comprehensive, the following list illustrates some of the key functional areas for which warehousing/distribution facilities should develop detailed, documented Standard Operating Procedures:
- Cycle Count Reconciliation SOP
- Shelf Replenishment SOP
- Back Order Clearing SOP
- Operational & Regulatory Controls Audit SOP
To read more, click here. | |
| |
| |
|
|
|